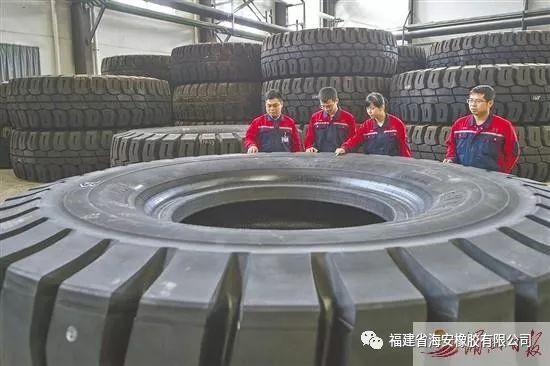
发轫于精微,执着于匠心。海安橡胶有限公司多年来攻克一道道技术难关,自主研发生产出“中国第一胎”——打破垄断创品牌
图:青年科研团队在车间研究分析新技术
如今公司成功研发出11种系列35个规格的巨胎产品,涵盖适用90吨到400吨的全系列矿用自卸车轮胎,先后获得国家发明专利2项、实用新型专利22项、外观设计专利12项。
昨日,在福建省海安橡胶有限公司,忙碌的生产线上,工人们身手熟练。一批新花纹全钢巨型轮胎整装上车,准备运往俄罗斯。技术中心实验室主任黄晶晶看着这一幕,回想起公司第一条全钢巨胎的研制历程,十多年来发生在团队身上的故事,如倒带般回放。
早在公司创建之初,人才队伍建设就被摆上重要日程。公司副总经理、技术中心主任黄振华高级工程师,是被公司发现并吸纳的第一批人才。与施大全、郭其焰以及当时大学刚毕业的黄晶晶,组成四人研发团队。
发轫于精微,执着于匠心,就是这样一支团队,不断壮大,历经酸甜苦辣,自主研制出属于中国人的巨型轮胎。在今年五四青年节前,该公司研发团队获得省五四青年集体奖章。
“起初,公司在设备、配方、工艺等方面都是空白,自主研发迫在眉睫。”黄振华回忆,当时,研发巨型工程轮胎,国外技术严格保密,国内又处于刚起步阶段,加上周期长、成本大,俨然一座座大山横亘在团队面前。
为了打破国外技术封锁的局面,在董事长朱晖的带领下,技术研发团队争分夺秒刻苦钻研,精益求精大胆创新,取得关键技术的重大突破。技术中心工艺室副经理许志展清晰地记得,在胎体结构设计方面,团队运用多种技术,创新设计出多款各类型胎面花纹。一次次的试验总结,一场场的脑力碰撞,团队破釜沉舟、推陈出新,在胶料配方、制造设备设计、硫化工艺设计方面,攻克了一道道技术难关。
2008年6月初,公司开始生产线的全面调试。由于许多设备是国内第一台套,启动试生产时困难重重。“董事长带着我们技术团队和生产骨干,吃住都在一线,四天两夜只睡了4小时。”黄晶晶是团队中仅有的两名女同胞之一,男同事经历的研发工序,她一项不落。令人欣慰的是,经过不眠不休的奋战,当月30日,海安第一条全钢巨胎成功下线。这就是被誉为“中国第一胎”的37.00R57巨型工程子午胎,打破了国际垄断。
然而,这仅仅是万里长征第一步。“由于技术尚不成熟,第一条轮胎的寿命仅能维持十几个小时,而当时国外生产的轮胎正常寿命是4000个小时。”黄振华说,该团队清醒地认识到差距,压力在肩。尽管处于亏本状态,公司仍一如既往地投入资金支持研发。迎难而上再出发,团队不断研究分析,多次到矿山勘查。经过几个月的持续试验,终于将轮胎的寿命提高到1000多个小时,实现质的飞跃。
2009年4月,海安橡胶轮胎生产技术获国家行业部委鉴定,成为国内唯一一家通过标准鉴定的生产厂家。此后,通过扎实的技术攻关和先进的设备配备,轮胎寿命不断延长到4000多个小时。2012年初,公司开始批量生产巨型轮胎。通过攻克一道道技术难关,如今成功研发出11种系列35个规格的巨胎产品,涵盖适用90吨到400吨的全系列矿用自卸车轮胎,先后获得国家发明专利2项、实用新型专利22项、外观设计专利12项。(上接A1版)随着研发力量的不断投入,越来越多的技术人才加入研发团队。团队22人中,大多数是80后,不仅有成熟的技术经验,也保持着研发所需的激情与创造力。配方室主任朱志鹏是土生土长的海安村人,从对本土企业的慕名,到加入其中、耳濡目染,他真切感受到研发团队的朝气蓬勃。在矿山一线“外营点”,他们下地勘查环境特点;在转鼓现场实验室,他们埋首“解剖”巨型轮胎……处处留下团队奔波钻研的身影。在公司研制的轮胎中,最小直径近3米,最大的4米多。与这样的“巨胎”朝夕相伴,团队中的每一人,目光更加坚定,思路更加清晰,心底更加自信。